No doubt for Maurizio Sandre and we could not even ask the first question: he really likes the sanding machine he bought from Imola-based Emc, it streamlines operations and allows to achieve better quality…
And if he says so, based on more than forty years of experience, you can be sure! Maurizio Sandre is a direct, frank person who doesn’t beat about the bush. He loves his work. We can say he really loves to work, he loves to fancy what else could be done, every day he tries to invent a process to be presented to his customers, and maybe some prospects, to show them that, with the right equipment and paint, they can create beautiful coatings, so beautiful that an Mdf board will look like a top-quality metal sheet or stone slab!
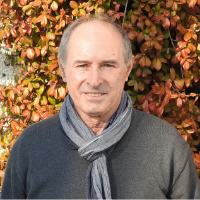
Maurizio Sandre
“Sandre Verniciatura was established in 1980,” he said. “I started as an electrician, I built the electric systems for bedrooms that sold like hotcakes in the Arab countries in those years! Turning beds, embedded stereo systems, tv sets hidden in cabinets… everything! At a certain point, this wealthy market disappeared: demand collapsed and I had to find new opportunities. I had no intention to go back building industrial electric systems with my staff, that was my original job, so I chose painting. Initially, it looked like a joke. We worked in an old mill, in disastrous conditions, but little by little we lifted off, riding the increasing popularity of coating. In 1996, we had our first hall here in Porcia, near Pordenone, then we gradually expanded into a small industrial business with 45 employees and revenues close to 5 million euro.”
“Painting is our job, and we do it well, whatever type of finish our customers request. We are also very good with “special effects”, as I call them, i.e. surfaces that don’t look like painted panels at all, but rather like carefully crafted metallic and special finishes. As a result, we are launching “Sandre Lab”, a collection of decors that we are presenting to interior designers, architects, furniture manufacturers, designers of high-end products, something exclusive, very peculiar.
Most of our work is for customers who demand top quality, famous brands or their subcontractors who rely on us to solve any problem, and also because we can always offer something new and different, and catch their attention. We have to raise the bar, to jump higher than others, if we don’t want to be cut off; this means being able to achieve better margins and avoid suicidal price wars. We have made clear choices: Sandre Verniciatura can “finish” more than six thousand square meters of materials with more than one thousand colors! Our plants handle twenty to thirty color changes each day, because we do not manage only orders for one or two thousand square meters, but also very small batches, just few pieces, maybe for special customers…
Customization has always been our keyword, that’s a gift and a curse. A gift because this decision has always secured a consistent intake of orders, a curse because you don’t always get the right reward. I must admit that, working with different customers, we have learned a lot, expanded our knowledge, become more flexible and ready to change, and to invest: we have a strong focus on new technology, as it allows to improve operations and speed; we have invested in a new machine to package finished parts and ship them without any risk; we have completely reorganized our IT operations, hiring a few young people who have encouraged us to “freshen up” some methods”.
Talking about investments, what’s your approach to technology?
“Technology is a key asset in our corporate vision; for our business, it is essential to identify the right machine and equipment: we process 3D parts manually, in two spraying booths, but we also have two carousel plants and a high-speed, versatile articulated robot. We paint using the products and methods requested by the customer, and we focus on two main stages: sanding and painting.
Sanding is often underrated in our job, but it is essential if you offer a wide range of finishes, including matte, brushed gloss as well as our “special” finishing. You have to sand the panel at the inlet station, then again after the first coat and maybe a few times more, so as to achieve the result specified by the customer.
Each day, we realize that, by modifying a specific step or detail, we can achieve even better results, and this approach has driven us to select flexible machinery”.
“We have always selected our machines very accurately,” Maurizio Sandre continued. “We have installed “Plano” by Emc, a sanding machine that handles 80 percent of the parts we paint. This machine is offering great satisfaction, but I must confess that I was a bit doubtful the first time I saw it. I have known Emc for many years. We have a longstanding partnerships and I daresay we are friends, but on that occasion they presented a really “strange” machine; however, we soon realized that it was very flexible, which is essential for us, and the huge benefits it could bring: we made some early tests and we were fully convinced.” It was designed with two pads that can operate with different levels of pressure and stiffness, so even with one belt with a length of 5,000 millimeters, we can count on a high number of variables to get exactly where we want! We can configure the machine so that the “harder” pad delivers much better results than a conventional pad, while the softer one reduces the depth of scratches. By crossing the grains, we achieve a result similar to a 400 grain belt, but maybe it’s just a 240 grain!
Furthermore, with a single belt, the machine is much easier to control, and its configurability allows to sand any material. I call it an “out of standard” sanding machine, it’s different from all the others, it is based on a peculiar concept, with technical solutions that make it really special. And I can assure you it is really easy to operate: we have assigned it to a skilled lady who knows our job perfectly, though she has never been a technology fan. Well, she handles “Plano” just like her smartphone, with excellent results. When the machine arrived, she was scared, but now she could not do without it!”
by Luca Rossetti
The Emc planar system
The “Plano” system by Emc in Imola, developed in collaboration with Liq Italia, is a painting system that does away with the conventional longitudinal system (wide-belt finishing) and the cross system (narrow-belt finishing), with the help of sophisticated electronics that allow to control a new rotary finishing system, consisting of a combination of three different systems: a wide abrasive belt, two fixed electronic pads and the rotation of the entire abrasive unit. With a single movement, it can create unrivalled finished surfaces with a never-seen-before gliding or planar effect (hence the name “Plano”).
Traditional systems operate on three adjustable parameters: conveyor belt speed; pad pressure; abrasive belt rotation speed.The new “Plano System®” by Emc adds a “4th dimension”, i.e. the rotation speed of the rotary unit, essential to achieve a flawless result. This new system completely changes the dynamics of the process: in traditional systems, the abrasive belt enters the panel, while with the solution developed by Emc, the panel enters the belt. This movement ensures the perfect finishing around all four panel edges, with a “seamless fillet” between the edge and the corner.
So, there are many reasons to choose the “Plano System®”: first, the planar finishing across the entire surface, thanks to the rotary system, offering the best finishing at the edges, an optimal management of corners and the complete elimination of accumulated paint along the edges.
Another noteworthy feature is the smaller footprint for sanding operations: with one single machine, you can execute operations that might require two or three sanding machines and the roller conveyors to move parts from one machine to another.
The capability to work “piece by piece” or with “full workbench” increases productivity, thereby outputting more square meters of pieces at the same speed.
All of this with simple and intuitive control via a 15.4-inch touchscreen interface, the possibility to save up to 200 settings and “continuous” process control, which can be modified quickly and precisely.
The Emc “Plano System®” also offers significant energy saving (up to 60 percent) and reduced belt consumption, as the rotary system guarantees uniform wear, thereby doubling the life of the belt.
And last but not least, you can finish any type of surface, including paint, melamine, polyester, Corian, rip-cut wood, cross-cut wood or mosaic.