A local excellent player has drawn the attention of a giant like Biesse Group, bringing their experience in machining centers specifically designed for wood constructions and composite materials.
“We belong to our territory, we are strictly connected to it, and we feel this every day, although Uniteam has now adopted a philosophy and a methodology that distinguish us from the handicraft company we used to be. Such difference is clearly visible in our products and in all our operations”. There was no doubt for Silvano Maddalon, Sales Director Uniteam, a production unit based in Thiene, when we asked him what it means for a Venetian company to be part of a big group.

Silvano Maddalon
“Being part of a big group like Biesse has enabled us to express our potential in a different way, with an industrial approach. We have adopted new rules, invested in specific market segments, implemented different product and business development concepts, a “team” approach, without wasting time and efforts on projects that are just “distractions” from an industrial viewpoint. Nevertheless, we are from Veneto and we will always be, preserving our enthusiasm, energy and passion for a specific way of working, which has always distinguished our territory.
I really believe that Biesse bring much added value, but our attitude, our approach to business has always been very similar: both companies are proactive, dynamic, keen on the management of business relations, on products, on organization. Such affinity has generated great synergies across our subsidiaries, helping us find inroads into important market that we could not even approach in the past, as we needed a “heavy” business card to have a credibility beyond the effectiveness of our machines.
Uniteam has always exported 70-80 percent of production: with Biesse, we can look further and build on our growth, addressing the entire world. This is how our original spirit has evolved, with strong roots in our traditional energy and working capacity, now combined with enhanced organization and a “one company” approach shared with the rest of the Biesse galaxy”.
More wood or composites?
“Right now, I would say 65 percent of our products go into wood constructions. At group level, we are also recording significant growth in plastic material processing, from drilling to cutting, plus the Biesse machining centers, of course. We have started to collaborate with Fraccaro, a pneumatic press manufacturer, in the thermo-forming sector, but the most interesting business is definitely wood constructions: in recent years, this sector has really exploded and it keeps expanding even in the difficult period we are experiencing.
We are renowned for our capacity to machine laminar beams and Clt (cross laminated timber) panels; this construction method has opened up the business of wood constructions to many companies, also because it is very popular among designers and engineers, who have recognized the benefits of this wood construction method.
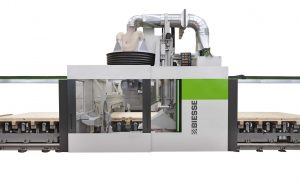
Uniteam “Clt 400”.
We are also working with timber frames, using a five-axis machine that can produce frame parts and elements faster and more cost effectively. We know this construction method very well, it offers great benefits, but it also has significant constraints, including the fact that you cannot exceed a certain number of levels. These techniques are very popular in Northern Europe, Australia and New Zealand, and in the United States, but their growth potential cannot compare with Clt; the latter has not even suffered during the months of the pandemic, it has continued to grow, recording very positive trends in France, Germany, Norway and the United States. We have developed great skills in the use of digital tools to offer demos, illustrate our solutions, present our specialties… this way of working will be precious in the future, when the events of recent months will be just a bad memory”.
You mentioned the United States, where you have been selected by a construction industry giant like Katerra…
“That’s true. Katerra is a huge player, born to be a leader in the wood construction business and beyond. We got in touch, we analyzed their needs and we have seen them grow into a giant that, in few years, has become one of America’s most important manufacturers of furniture and houses. As Biesse Group, we cover both of their business areas, i.e. furniture and Clt machining.” We have supplied two machining centers “Uniteam Clt 400” for their new plant in Spokane, Washington, an incredible unit in terms of dimensions, organization and production volumes. We installed two almost identical machines: it was an amazing experience and an excellent reference to become stronger and stronger in a key market like the United States. Moreover, wood is increasingly used in multi-storey buildings, so there is strong demand for bigger and bigger timber beams and pillars to replace concrete. Many players, including Katerra, are moving into this direction, and for us, a specialist in large beams, new opportunities are arising: it is not mere chance that we have been working very well in Canada and the United States recently…”.
How important is it to develop new machines in your destination markets?
“Very much. I can tell you that we are working hard on new projects, machines to process large beams as well as smaller elements that can be used to build frame walls, as mentioned before. This is new for Biesse, it’s a machine we have incorporated into a production line built with a French partner, that has aroused much interest.
Our beam processing machines have always drawn attention; equipped with suitable lifting and handling systems, they can process panels up to three meters; we can load beams automatically from a buffer station, or we can add vacuum devices to lift a huge Clt panel and manipulate it on the worktable to execute all necessary operations with high accuracy.
We have enhanced our specific machines for Clt, equipping the most performing models with motor-driven benches and two working units. We are innovating our loading and unloading systems to create high-performance inline solutions with high automation levels, to meet the increasing request to integrate all operations in lines made up of several machines that can handle the entire cycle from raw panel to finished wall, ready to be loaded into a truck and delivered to the construction site.
This is an interesting development that we can pursue more easily with a group organization: we must design more and more integrated solutions, including automation and software, that can acquire and “digest” architectural drawings, as well as communicate with all enterprise management and reporting systems. Today, you cannot simply focus on the power spindle speed, as in modern plants and machines, the key parameters are setup times, loading, unloading, zero-point detection, and handling panels weighing a few tons.
And to develop a successful concept, it is essential to talk with customers who process panels and those who produce them: there are producers from countries were wood constructions have ancient origins and companies have much more experience than we have. Think about Germany, Austria and many more markets where, starting from Thiene, we can play and will play a role, also because we are part of Biesse! We decided to take up the challenge of timber constructions a few years ago, when we were still a small business, and with Biesse we have invested and we will keep investing in an ambitious “product roadmap”, expanding our portfolio for glulam beams, large pillars, and possibly strengthening our focus on prefab houses, a business that involves many technologies we can gradually approach. This business is currently dominated by few players, but there is space for more, possibly with a suitable offer to attract even small and medium companies that will decide to adopt certain technologies”.
Engineering and design are critical in this business…
“Timber constructions, from one-family houses to huge buildings, require solid engineering to maximize the prefabrication phase and then to speed up mounring and minimize errors in the construction site. I really believe that these three factors are the keys to the future success of wood constructions. We are ready: our machines effectively meet the requirements of working “upstream” – although human intelligence and labor are essential – and in most cases, any information generated by architectural software is “crunched” by the machine to produce all sorts of products – such as beams or Clt panels – with a very high level of automation”.