The first issue of the new year launches the presentation of all the solutions awarded at the latest Xylexpo. The first solution illustrated by Matteo Simonetta, head of the technical office at Acimall, is signed by Paoletti Energy.
The Xylexpo Innovation Award in the solid wood processing category was assigned to the “Iglueing PUR hyper” solution by Paoletti Energy, based in Belluno. The device is designed to sprinkle one-component polyurethane glues in horizontal gluing systems and optimization lines for finger joints.
I talked with Pierluigi Paoletti, owner of Paoletti Energy, and Alessio Costantini, owner of L.A. Cost srl in Perugia, the first customer using the new gluing solution. I started by asking the latter to introduce his company.
“Our company L.A. Cost manufactures X-Lam panels and glulam beams, including curved and large-span elements, suitable for all kinds of buildings; we also offer turnkey installation services with the Costantini Legno brand. The company has been operating in this business for more than 30 years, emerging as one of the most important players in Italy. In recent years, the interest for wooden houses has increased significantly, both in Italy and in Europe. So, in this period, our core business is focused on wooden houses with high energy efficiency standards.
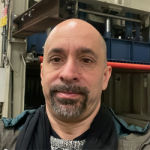
Pierluigi Paoletti
In a factory with a 24-thousand-square-meter surface and two separate plants, we can produce 100 cubic meters of beams per daty, while the X-Lam panel line at full load can reach up to 500 square meters of panels each day”.
Mr. Costantini, which are the benefits of the new gluing system?
“Within a technology innovation plan involving all our production lines, launched in 2022, especially for gluing the layers of X-Lam panels, we were attracted by the innovative gluing system created by Paoletti Energy, we wanted it, and we installed it in November (so, shortly after its presentation at Xylexpo, editor’s note).
We have been testing its effectiveness for a few months: it has significantly increased the efficiency of our production line. The gluing time is dramatically shorter compared to previous systems, and moreover, unlike the latter, we have more accurate control over glue consumption, as well as the consistent dispensing of glue across all panels.
These are the factors that have driven us to choose the new gluing system. Another interesting element was the transition for melamine to polyurethane glue, which releases no additives or formaldehyde, so the product is less harmful.
The reduction of cycle time was achieved not only for maintenance, but also for the gluing process itself. The dispenser is more effective, and changing the type of glue has also helped us reduce the process time, as well as the optimization of the movements executed by the gluing aggregate: with one pass, we can spread glue over the entire surface panel. Gluing time has been cut more less into half, compared to previous systems”.
“The process – added Pierluigi Paoletti – can become even faster, as the open time of polyurethane glues is shorter. For cleaning and maintenance, the system of individual head-valves that can be extracted separately allows to carry out ultra-fast maintenance, within tens of seconds, without having to dismantle the aggregate or its elements; and, each valve can be replaced quickly, so you don’t need to wait until it’s cleaned.
The high-pressure system minimizes the dirt on panels and distributes the adhesive more evenly, so with less waste. The gantry to move the gluing system already existed, so we mounted the new technology onto it. The brushless motors driving the Cartesian axes can move the 2-ton gantry at a speed of 70 meters per minute”.
You mentioned solutions that sound new to me: can you sum up all the inovative technical features of this system?
“The “Iglueing PUR hyper” system is comprised of a valve unit with independent heads, each driven pneumatically by a solenoid valve, according to the width of the parts to be glued. The centerline distance between the dispensing nozzles is ten millimeters, while the valves are 50 mm wide.
The valves are fastened to the manifolds by screws, so that each valve can be removed independently for faster maintenance, while also streamlining ordinary checks of the manifold units. The latter are anchored onto an extruded aluminum profile by means of brackets.
The “Hyper” term refers to the model with pumping system (with one or more pumps) operating at high pressure, up to 100 bar. This allows to use smaller diameter piping and ensures accurate and consistent glue dispensing over time, with glue savings in the range of 15 percent at least.
The device features a lubrication system with an oil tank constantly connected to the valves, to keep the seals lubricated and flowed with oil and avoid the ingress of air and moisture, thus preventing resin polymerization around the valve piston. The piston is covered with Teflon to streamline maintenance and to keep the chambers tight”.
“The valve body is a pneumatic actuator that drives a piston which dives into the glue tank, where a head with a closing pin stops the flow”, Paoletti continued. “This innovative system, with one pin for each nozzle, minimizes glue waste and ensures the tightness of the valve chamber.
The dispensing head is made of polymer material, which prevents the glue from sticking and ensures quick and efficient cleaning. Furthermore, the head can be easily extracted, with a quick-release system for ordinary maintenance and fast cleaning, plus the possibility to replace the head, thus avoiding downtime during the production cycle.
The device tightness is guaranteed by a system that closes the pins even when electricity or compressed air are not available. Dedicated software controls the automatic cleaning process for each valve body and head”.
Mr. Paoletti, which additional developments are you planning for the L.A. Cost plant?
“We have already prepared the line for the next implementation step, namely the addition of automated loading to increase our production capacity further, possibly the highest capacity in Italy. This will be combined with great flexibility: today, you must produce what is needed, when it is needed, fast and with no waste, delivering panels in the required dimensions, all different, with no scraps. With a numerical control electronic system, glue can be dispensed where required, for as many layers as you need. We don’t make large panels that must be cut to size with plenty of scraps, we only make the panels required for each order: this ensures the biggest saving.
According to Industry 4.0 principles, the plant is connected to the enterprise management system. In this way, we can supervise the entire X-Lam panel production process and monitor all production parameters in real time: how much glue is dispensed, how many panels we make, and even how many valves open. Upstream of this plant, we still have a finger jointing plant that has been up and running since the year 2000.
Glue saving compared to previous systems is approximately 15 percent, up to 20. More accurate figures will be available as soon as the management system will be tuned up. Also switching from MUF to PUR glue, featuring different cycle time, has led to such saving levels. Putting everything together, we can increase our production fourfold”.
How did you develop this idea and the project?
“Paoletti Engineering was founded in 1962 and has been manufacturing plants for glulam beams and X-Lam panels for more than twenty-five years. We have always seen defects in the gluing systems of these plants, so we started to also produce the gluing system ourselves; our lines have become more efficient overall, and no competitor builds all the machines of a line like we do. We are a small company, but we make the entire packed in house. This has allowed us to acquire the full knowledge of all process stages, especially the pressing phase: we know about the issues and the pressing time. Our know-how about press construction and gluing operations has combined with the experience of L.A. COST in panel production. Having collaborated for decades, I could offer the next step of this new gluing system: Costantini took up the challenged, he trusted us, and we build a custom solution based on standard elements with a modular concept.
Each valve is designed by Paoletti Energy and is suitable not only for panels, but also for finger jointing. Our system injects the glue directly onto the surfaces to be joined, avoiding the use of combs to spread the glue. in this way, we save approximately one hour each day to clean the machine and its tooling, and we also minimize the use of solvents, which is restricted to extraordinary maintenance”.
Which are the prospects to expand this system?
“Many customers are requesting the new gluing aggregate to install it on their machines, including machines from other vendors. Press manufacturers also require the gluing system for composite wood panels and insulating materials like polystyrene, so not only in the construction industry. As you see, great versatility…”.
Matteo Simonetta
Acimall Technical Office director
costantinilegno.it
paolettienergy.com