During Xylexpo Digital, the platform that put Xylexpo on the air, ample space was dedicated to materials, processing and in-depth studies carried out with Catas, the most important European testing and certification laboratory for the wood-furniture supply chain. After the first event, dedicated to solid wood, this time it was the turn of panels, the ‘heart of every piece of wooden furniture’.
Panels are the soul of a piece of furniture and the quality of wood-based panels is always a ‘hot’ topic that we have eviscerated, thanks to the help of Catas, the most important European testing and certification laboratory for the wood-furniture supply chain, during the last edition of Xylexpo Digital, which broadcast the Milan biennial. Showing us around the world of panels and the tests carried out to guarantee their quality were Franco Bulian, director of Catas, Daniele Bergamasco, head of the chemical laboratory and deputy director of Catas, and Paolo Tirelli, head of the mechanical testing laboratory.
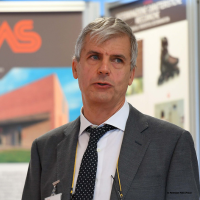
Franco Bulian
‘After having dealt with solid wood,‘ explains Franco Bulian with reference to the first “episode” of Catas’ in-depth studies, which aired during Xylexpo and which you can find on the event’s YouTube channel and in the last issue of Xylon, ‘ this time we are talking about the wood-based panels that derive from this starting material.
Panels today represent the skeleton of all furniture that is made, domestic, office. They all have a soul within them which is made up of these very panels. A fundamental role and, as you can easily imagine, panel manufacturers have to pay great attention to their characteristics to make sure that they are suitable to withstand the stresses that the finished product will undergo once in use.
There are several tests to which panels are subjected: mechanical, such as flexural strength, internal cohesion or density profile, and chemical, the study of the panel’s composition, which is particularly relevant to obtain a product that is as strong, reliable and durable as possible. ‘Today, more and more recycled materials are used, which are derived from the end-of-life of other products: this means that there are also other substances that are not typical of the ‘original’ wood. Today, some substances that could have been used years ago are now banned, so it is necessary, for example, to check that there are no substances inside that cannot be used today’.
Not only that, another check concerns formaldehyde emission. ‘The formaldehyde emission of a panel,’ explains Franco Bulian, ’ derives from several factors. Firstly, from how the panels are made, secondly from the resins, types and quantities, used to bind the various particles and wood fibres. These resins emit formaldehyde over a long time and it is important to evaluate them‘.
CHEMICAL TESTS
‘There are therefore a series of tests, verifications and certifications that guarantee that the product complies with the requirements of the regulations,’ explains Franco Bulian. “In the chemical laboratory, we carry out panel analyses to check not only formaldehyde emissions, but also the content of possibly hazardous substances. To best explain what chemical tests we carry out in the laboratory, I give the floor to Daniele Bergamasco, head of the chemical laboratory and deputy director of Catas‘.
‘What we do in this department,’ Daniele Bergamasco tells us, ‘ is the determination of the formaldehyde present in wood-based panels, which are normally used to create furniture and then sold in Italy and abroad, and the determination of those substances that we can find inside the panel, which must be verified and regulated.
We are in a delicate historical moment, which requires the use of recycled materials, which in the case of wood means working with previously treated wood. This means that, once delivered to the company to be reprocessed, the panels must first be cleaned and washed so that there are no hazardous substances for the end user. What do we do at Catas? We make sure that any type of panel we test can get ‘into homes’ in the safest way possible”.
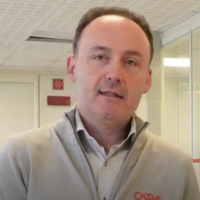
Daniele Bergamasco
Formaldehyde is a gas emitted from panels due to the breakdown of the glue used to join the individual units that make up each panel. This compound is recognised as a carcinogenic substance and its emission is regulated by law.
Catas’ work consists of assessing whether the formaldehyde content released by the panels is within the limits set by law, thus guaranteeing the safety of the finished product for consumers.
In addition to formaldehyde, contaminants within the panels, including heavy metals and asbestos fibres, are monitored to ensure that the end product meets quality and safety standards. A Catas-certified panel is safe for domestic use and complies with legal requirements, guaranteeing the consumer a reliable choice.
Formaldehyde analysis is performed using standardised gas analysis equipment, which in just four hours verifies the panels’ compliance with even the most restrictive Italian and European regulations. This test confirms that the panel meets current safety standards.
The test facility includes steel test chambers, designed to simulate the environment of a normal home, maintaining stable temperature and humidity conditions. Panels are prepared and cut according to the type of analysis required. Inside the chambers, samples remain for a period of 7 to 28 days, during which daily air samples are taken to monitor formaldehyde emissions. At the end of the 28 days, the results obtained make it possible to establish whether the panels meet Italian and European safety regulations.
MECHANICAL TESTS
From chemical to mechanical tests. ‘At the moment, the most commonly used materials for forming panels are chipboard, mdf and plywood,’ explains Paolo Tirelli, head of the Catas mechanical testing laboratory. ‘At Catas we ‘characterise’ these panels, going to ‘stress’ the materials, to monitor the loads and understand what the resistance is, when they break, where they break, and above all ‘how’ they break. Often the how they break is more important than the point at which they break.
The point of these tests is precisely to understand the strength of the panel: of a screw on the panel, or of the internal cohesion to understand if the particles and fibres have been evaluated well, the quality of the plywood. A 360 assessment to understand what we can call the performance of the panel’.
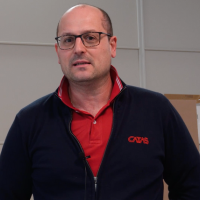
Paolo Tirelli
The challenges for the panel industry, as Paolo Tirelli himself explained, are well defined in the medium term, especially for those who observe the sector with an impartial eye. One of the main aspects is sustainability, understood as the use of recycled wood for panel production. However, these materials tend to weigh heavily. At the same time, regulations are directing companies towards lighter solutions, such as chipboard or sandwich structures made of wood-based materials. Sustainability therefore combines with the need to lighten the product, creating an initial area of innovation for the future.
Another challenge concerns the need to update the technical regulations applicable to the sector, especially those relating to the mechanical characteristics of panels, which have remained unchanged for over thirty years. Currently, there are regulations on board embossing, but the permitted limits are too high, which is problematic for the wood-furniture sector. In fact, a panel with a high degree of buckling already at an early stage tends not to meet the required deflections for shelves, creating problems during use. It therefore becomes essential to integrate sustainability and mechanical performance in order to obtain better and more durable products.
The third challenge concerns the association of panel performance with the processing steps. This aspect places new demands on standards, as there are currently no established methods for assessing the quality of panel performance during cutting or for dealing with difficulties related to elements such as blades, tools, or even the presence of sand in the panel itself. This is still an unexplored area, which will require in-depth research and new regulations in the coming years to ensure both the quality of the workmanship and the robustness of the final product
‘As we have said many times,’ concludes Franco Bulian , ’panels are the heart of all furniture being made today. We have seen different characteristics, safety, mechanical components.
The characteristics of the panels also have a high impact on the processing that is then carried out on the materials. Let me give a simple example of a chipboard panel.
The structure of the chipboard, how ‘grainy’ it is – for example – in the middle part, can have a major effect on the edging phase, affecting gluing, among other things. We must never forget that these are the materials we work with and they can have a certain variability, so we must be careful, consult the technical data sheets and do some checking, because some variability may depend on the wood species or recycled materials. Checking is essential to then ensure that the product will meet the needs of the market and consumers.
catas.com
xylexpo.com
Click here to watch the episode online!