È davvero emozionante ritrovarsi circondati da divani, cuscini, legno, stoffe, imbottiture, e pannelli che a poco a poco si trasformano in centinaia di divani, l’uno diverso dall’altro. Competenza, esperienza, tecnologia, organizzazione. Questi i pilastri cu sui si fonda Atl Group di Imola.
Dopo qualche anno siamo tornati a Faenza, a vedere gli ultimi investimenti in tecnologia decisi da Atl Group per il suo grande insediamento industriale, il cuore produttivo di questo sistema. E benchè oramai sappiamo cosa ci attende, è sempre un piacere fare un giro in questo enorme impianto interamente vocato alla produzione di divani. Ci sono pochissime realtà come questa: poco meno di 600 addetti, 100 milioni di fatturato e tre unità produttive: oltre ai 45mila metri quadrati di Faenza ce ne sono altri 10mila a Bertinoro, dove nasce la produzione di alta gamma, e altrettanti a Forlì dove ci sono alcuni magazzini e la sede operativa di Cipes, la cooperative per il taglio del poliuretano da dove questo “impero dell’imbottito” ha preso vita oltre quarant’anni fa.
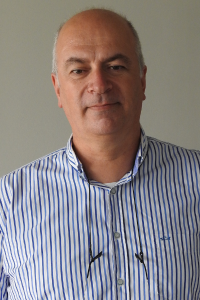
Claudio Benini
“Il posto migliore dove far produrre i tuoi divani” è il pay off che fa immediatamente capire di cosa stiamo parlando: Atl Group produce imbottiti per alcuni dei più bei nomi del mobilierato italiano (e non solo), divani e poltrone che sfoggeranno nomi d’alto lignaggio. Nell’enorme stabilimento di Faenza nasce l’intera produzione della forse più vista (in televisione) realtà della grande distribuzione di imbottiti, il cui segreto è ragionare per grandi numeri, grazie ai quali è possibile fare una buona qualità a prezzi decisamente contenuti. È qui che si tagliano il poliuretano e i tessuti, è qui che si cuce, si riveste, si imballa… è qui che c’è la grande falegnameria dove si lavorano listelli e profili in legno ma soprattutto si tagliano, sagomano e fresano migliaia di pannelli di truciolare e multistrato.
“La produzione è leggermente aumentata rispetto alla sua ultima visita”, ci ricorda Claudio Benini, direttore generale al quale tocca la responsabilità della produzione, della logistica, e della gestione informatica. “Oggi siamo a quota 1.300 divani al giorno fra tutte le unità del gruppo. Basta fare due conti per rendersi conto di quale sia la sfida più importante: disporre di un sistema perfettamente organizzato per fare in modo che tutte le parti, gli elementi necessari siano disponibili per essere assemblati nella nostra linea di produzione. Indispensabile essere assolutamente flessibili, avere tecnologie adatte, per quanto cerchiamo di organizzare la produzione dei semilavorati per piccoli magazzini intermedi, polmoni giornalieri che ci consentano di non fermarci mai: quando si parla di queste quantità e soprattutto di questa grande variabilità è impensabile poter contare su grandi magazzini e bisogna scegliere impianti e macchine adeguate per seguire il più possibile la logica del “just in time”.
Le dicevo che negli ultimi anni sono aumentati gli “elementi in bianco” che produciamo ogni giorno, ma il vero problema è la complessità che sta dietro a questi numeri: i tempi di lavorazione sono cresciuti in modo proporzionalmente esponenziale, perché è cresciuta la domanda di divani più “articolati”, con forme più sagomate. È la tipologia dei pezzi che produciamo che ci porta a investire in tecnologie più performanti e flessibili che ci fanno recuperare quel 30 per cento di lavoro in più che ci ritroviamo a fare”.
“Quando si fanno certi numeri – prosegue Benini – gestire la produzione non è semplice ed è indispensabile guardare prima di tutto all’efficacia, ben sapendo che il risultato finale è comunque fortemente condizionato dalla efficienza. E, come le ho già detto, più che i volumi è la variabilità a dover essere governata, perché per ogni nuovo divano che si trova in negozio dobbiamo progettare, tagliare preparare listelli, profili, sagome, cuscini, imbottiture e pezzi di stoffa diversi.
Siamo dei terzisti, dei bravi terzisti: il mercato chiede modelli sempre diversi e questo non può che alimentare l’elenco di ciò che facciamo. È il nostro mestiere dare al mobiliere, alla distribuzione ciò che ci chiedono, possibilmente apportando quelle migliorie che la nostra oramai lunga esperienza ci permette di poter consigliare”.
Atl Group è cliente affezionato di Scm per quanto riguarda le macchine operative nella grande falegnameria, dove negli ultimi tempi sono arrivate due “new entry”: la nuovissima sezionatrice angolare “gabbiani a2” e un centro di lavoro “accord 40 nst” definito proprio sulle esigenze della produzione di parti per i fusti dei divani.
“La nuova “accord” ci permette di ampliare la nostra capacità di lavorazioni nesting, rendendo questa fase del processo molto più fluida rispetto a prima”, ci dice Benini. “Possiamo lavorare su pannelli di grande formato con due teste contemporaneamente, così da poter ottenere elementi diversi o raddoppiare la produttività, grazie anche alle elevate velocità che questo centro di lavoro può raggiungere. Rispetto agli altri centri Scm con i quali lavoriamo, questo lo abbiamo voluto con una configurazione diversa, che ci permette di avere una stazione di uscita a metà della macchina, una polmonatura che consente alla macchina di poter gestire al meglio il flusso di lavoro. Abbiamo richiesto alcune modifiche sia per la fase di carico – così da poter facilmente gestire anche elementi di dimensioni più contenute, una opportunità molto utile quando si lavora con il multistrato – che per lo scarico, dove abbiamo aggiunto un altro polmone per rendere meno “pressanti” le tempistiche di prelievo dei pezzi tagliati finiti, che possono anche essere molti, senza dover aggiungere persone.
Velocità e produttività hanno raggiunto livelli talmente elevati da rendere necessario un doppio tappeto in uscita in modo che l’operatore abbia tutto il tempo per prelevare il pezzo finito mentre la macchina continua a lavorare senza presidio nelle stazioni intermedie.
Questo centro ci offre ben altre prestazioni rispetto al passato, grazie a velocità ma soprattutto a una dinamica diversa, a percorsi meglio ottimizzati, lavorando fino a tre pannelli sovrapposti. Si tratta indubbiamente di una cella flessibile e potente”.
Avete comunque investito anche nella sezionatura “tradizionale”…
“Questa è la quarta sezionatrice “Gabbiani” che entra in Atl Group. Questa volta abbiamo investito in una “angolare” pensata per una produzione più flessibile e ottimizzata di semilavorati, componenti per i fusti che possa conciliare la necessità di trovare il miglior compromesso possibile fra lotti minimi e una produzione sempre più frammentata. Non possiamo certo ragionare in termini di “lotto uno”, tagliare i pezzi che servono modello per modello, sebbene questa nuova “gabbiani a2” sia sufficientemente flessibile e soprattutto estremamente veloce sia nel taglio che nella movimentazione dei pannelli. Tali caratteristiche che ci hanno permesso di aumentare la produttività di questa fase del processo di un buon 30 per cento.
Una macchina versatile e potente, che ha dato un forte contributo al nostro modo di lavorare: se prima eravamo spesso in affanno, ora la produzione di buona parte dei nostri semilavorati può essere gestita in tutta tranquillità e per una programmazione ferrea come la nostra è un plus molto importante.
Non dimentichi che stiamo parlando di una macchina che può lavorare più pannelli sovrapposti per ricavare parti che dovranno poi essere assemblate ad altre per costruire il telaio di un imbottito, abbinate con elementi in poliuretano, acciaio, gomma… la precisione è un valore al quale non possiamo rinunciare e questa nuova sezionatrice angolare ce la garantisce.
Diciamo che è un completamento del nesting o, se preferisce, il nesting è un completamento della sezionatura: queste due lavorazioni sono alla base della preparazione di tutti gli elementi ricavati da pannello e vi ricorriamo a seconda delle esigenze, della necessità di avere parti solo squadrate o con sagomature, fresate o altri interventi che ci permettano di ottenere un elemento finito, pronto per essere assemblato. Stiamo parlando di due modi diversi per arrivare, in sostanza, allo stesso risultato; ovviamente con tempi e scarti diversi…”.
Soddisfatti, dunque…
“… con Scm abbiamo un rapporto di lunga data: quasi tutte le nostre macchine hanno il loro marchio. Una collaborazione fondata sulla conoscenza e sulla qualità del prodotto e soprattutto della assistenza che, per una realtà come la nostra, è un valore assoluto”:
a cura di Luca Rossetti
LA SEZIONATRICE ANGOLARE “GABBIANI A2”“
La “Gabbiani a2” per Atl Group ha una sporgenza massima della lama di 125 millimetri ed è attrezzata con il nuovo gruppo “Saw set” per il cambio utensili automatico, allineatori laterali motorizzati e un sistema automatico di etichettatura del pannello a bordo spintore prima della fase di taglio. Il dispositivo “Flexcut 1D” consente di eseguire schemi di taglio complessi in tempi estremamente ridotti, mentre “Zero dust system” garantisce la massima pulizia dell’area di lavoro, grazie a un sistema automatico di saracinesche a settori che intervengono per contenere le polveri e garantirne la completa aspirazione.IL CENTRO NESTING “ACCORD 40 NST”
Il nuovo “accord 40 nst” è un progetto tecnologico “su misura” per Atl Group, una cella altamente personalizzabile che garantisce un’elevata produttività con una automazione di alto livello.
La cella può lavorare tre pannelli contemporaneamente grazie all’esclusivo spintore ad ingresso macchina, che consente di caricarne fino a tre, e ai due gruppi operatori paralleli indipendenti, ciascuno dei quali equipaggiato da una testa a forare e da un elettromandrino ad alta potenza. Il doppio tappeto in uscita permette di gestire al meglio lo scarico dei pezzi lavorati, alla luce della notevole rapidità con cui viene effettuata la lavorazione: l’operatore ha così tutto il tempo per prelevare il pezzo finito mentre la macchina continua a lavorare senza presidio nelle stazioni intermedie.