Un traguardo importante per un compleanno che non si festeggia “tutti i giorni”. Abbiamo avuto il piacere di intervistare Dario Camporese, titolare di Saomad, per ripercorrere insieme a lui la storia dell’azienda padovana e vedere che cosa “bolle in pentola” in quel di Campodarsego…
Una lunga storia alle spalle, ma tanti capitoli ancora da scrivere davanti. La storia di Saomad parte da lontano: da un’Italia diversa, sicuramente meno digitale, ma forse più vera, più concreta, più reale e meno “virtuale”. Erano gli anni del boom economico che stava ricostruendo le macerie di un capitolo buio, anni in cui dalle idee fiorivano nuove iniziative, nuove aziende, nuovi orizzonti e si formavano (o si riformavano) distretti ricchi di quella che, a distanza di oltre mezzo secolo, possiamo definire tradizione.
E la storia di Saomad parte proprio in un contesto che, negli anni, è diventato uno dei distretti industriali di riferimento (non solo per l’industria della lavorazione del legno) e una fucina di idee.
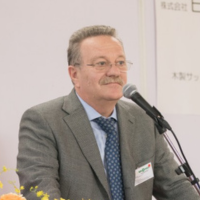
Dario Camporese
E per raccontare che cosa è stata e che cosa è oggi Saomad, l’azienda padovana specializzata nella realizzazione di tecnologie per la produzione di serramenti in legno, abbiamo avuto il piacere di intervistare Dario Camporese, il titolare, la seconda generazione che porta avanti l’eredità di un’azienda che in questo 2023 spegne 65 candeline.
“La nostra storia comincia nel 1958 – ci racconta – quando mio padre decise di aprire l’azienda. Ripensandoci oggi era tutto completamente diverso. Facevamo macchine, mi conceda il termine, più tradizionali, per lavorazioni meno complesse e soprattutto inizialmente eravamo votati per lo più al mercato nazionale.
Poi la situazione è cambiata, le richieste dei clienti sono aumentate, il nostro mercato si è espanso. Abbiamo inserito nuove macchine, abbiamo cominciato e ci siamo specializzati nella produzione degli infissi, dalle tenonatrici manuali alle prime profilatrici.
E se abbiamo raggiunto questo punto lo dobbiamo alla nostra costante voglia di innovare, di cercare nuove soluzioni, di puntare sulla tecnologia. Una scelta e una attitudine che ci ha portato a lavorare per primi sugli angoli, partendo da macchine più piccole e arrivando oggi a fare delle linee complete in grado di lavorare con rapidità e qualità”.
Una lunga storia che si è dovuta confrontare anche con un triennio decisamente “particolare”…
“Esattamente. Negli ultimi tre anni la situazione sicuramente è cambiata. Le problematiche sono state diverse, dalla pandemia con le sue conseguenze, alla complessa situazione geopolitica che ha provocato le note difficoltà nel reperire i materiali, l’aumento dei costi. Una situazione che ha colpito tutte le aziende chiaramente. Come abbiamo reagito? Ci siamo rimboccati le maniche, abbiamo cercato di programmare ancora meglio la produzione, le consegne, in modo da poter avere sempre un quadro preciso che ci facesse lavorare “in anticipo” di mesi, potendo così ordinare il materiale con largo anticipo. E posso dire che, al netto di qualche ritardo che è stato fisiologico, siamo riusciti a fare un ottimo lavoro”.
In che direzione sta andando il settore?
“Credo che la direzione che ha intrapreso l’industria della lavorazione del legno (e non solo) e quella che sarà la strada da percorrere continuerà ad andare verso una sempre maggiore automazione. Soluzioni che siano in grado di ridurre il dover ricorrere a più manodopera, linee che possano lavorare anche 16 ore al giorno senza uomini, riducendo i rischi di un lavoro che, nonostante tutto, è usurante, e affronti quelao che è la grande difficoltà del nostro settore e del nostro distretto: trovare personale specializzato.
Questo – prosegue Dario Camporese – sta dettando la linea e cambiando anche le tendenze. Le richieste dei clienti si stanno muovendo, di conseguenza, sulla ricerca di linee complete che riescano a lavorare il prodotto e ottenere il pezzo finito nel minor numeri di passaggi ed evitando di fare lavorazioni fuori dalla linea. Una richiesta che – specialmente negli ultimi anni – è diventata di tutti, con l’obiettivo di ridurre – oltre al ridurre la manodopera – anche i fermi macchina”.
Flessibilità, automazione e…sostenibilità?
“Sicuramente il tema della sostenibilità sarà una delle parole chiave che ci accompagneranno anche nel futuro. E l’anno appena passato ci ha dimostrato una volta di più come il risparmio energetico e l’attenzione al ridurre gli sprechi siano due punti su cui non si può più aspettare. Ma in Saomad (sorride, ndr.) siamo sempre stati attenti a questi aspetti e la nostra gamma di macchine attuali garantisce un risparmio energetico di circa il 40 per cento rispetto al passato. Insomma, non ci siamo fatti trovare impreparati…”.
Ci sono ancora margini di miglioramento?
“Sicuramente sì. Abbiamo fatto un ottimo lavoro, ma sono sicuro che si potrà sempre migliorare. Come dicevo, quello della riduzione dei costi è un aspetto che coinvolge tutti, oltre che a livello ambientale, anche a livello economico. Non le nascondo che l’attenzione dei nostri clienti sui consumi delle varie macchine sia aumentata, ma è normale. Se fino a qualche anno fa il costo dell’energia era rilevante, ma non particolarmente impattante, adesso è diventata una voce di bilancio importante. E questo ovviamente spinge a investire nella ricerca per soluzioni sempre più performanti con un ridotto consumo di energia”.
Abbiamo accennato al tema dell’innovazione. Che cosa “bolle in pentola” in Saomad? Quali novità presenterete nel prossimo futuro?
“Abbiamo da poco ultimato e stiamo per lanciare “Woodpecker Performance”, un centro di lavoro a controllo numerico per la realizzazione di serramenti in grado di consentire lavorazioni “just in time”. Il nome stesso vuole mettere in evidenza qual è la caratteristica della macchina: performance, un’alta qualità di lavorazione per una macchina in grado di avere un alto rendimento anche sotto forte stress e con lavorazioni intense. Per darle un numero, sarà una macchina in grado di lavorare un pezzo ogni 45 secondi, riuscendo a lavorare anche dieci pezzi contemporaneamente, riducendo al minimo la presenza degli operatori. Una novità che – ne siamo certi – sarà particolarmente apprezzata sul mercato.
Ne siamo certi perché le innovazioni più funzionali ed efficaci sono proprio quelle che seguono le richieste dei clienti e del mercato”.
Voltandosi indietro e guardando avanti che cosa si sente dire a sé stesso e a chi ha collaborato con lei in questi anni?
“Sessantacinque anni di attività sono un traguardo importante, un punto che non tutte le aziende raggiungono in Italia. E noi, dopo tutto questo tempo, ci siamo guardati indietro e ci siamo resi conto di quanta strada abbiamo fatto da quando mio padre, nel 1958, diede il via a questa grande avventura. Tanta strada, tanto impegno, sacrificio, passione per quello che abbiamo fatto e facciamo anche oggi. Che cosa possiamo dirci oggi, dopo 65 anni? Che siamo stati bravi. Che la voglia di fare è stata tanta e che se abbiamo raggiunto certi traguardi dobbiamo farci i complimenti. Ma ci tengo a sottolineare che questo non è un punto di arrivo, è solo un’altra tappa nella nostra storia”.
a cura di Francesco Inverso
“WOODPECKER PERFORMANCE”
“Woodpecker performance” è un centro di lavoro a controllo numerico per la realizzazione di qualsiasi tipo di infisso in legno. Questa soluzione fa delle alte performance il proprio marchio di fabbrica (in quello che, scomodando il latino, potremmo definire “nomen omen”, ndr.). Da Saomad, infatti, ci hanno spiegato che questa macchina può lavorare dieci pezzi contemporaneamente, garantendo il pezzo finito in 45 secondi.
“Woodpecker performance” può lavorare pezzi alti da 15 a 160 millimetri, con una larghezza tra i 50 e 240 millimetri e un’altezza compresa tra 260 e 6mila millimetri.
“Rispetto alla gamma “Woodpecker “– ci spiega Dario Camporese – abbiamo incrementato il sistema di carico e scarico e il magazzino utensili, che adesso ha una capacità di 750 utensili. Inoltre le tre caratteristiche che rendono speciale “Performance” sono le polmonature di carico, il magazzino utensili e la capacità di lavorare più pezzi alla volta, riducendo notevolmente i tempi di produzione”.