Lo andiamo scrivendo oramai da anni: “sostenibilità” sarà una delle più importanti e frequentate parole d’ordine del prossimo futuro e adeguare qualsiasi prodotto o servizio a questo principio sarà una delle più forti spinte alla innovazione. Esattamente come è successo alla Ormamacchine di Torre Boldone (Bergamo).
“Mai come di questi tempi è necessario innovare prestando la massima attenzione a valori che stanno sempre più condizionando in positivo qualsiasi attività umana. Lo abbiamo fatto e lo facciamo quotidianamente anche in Ormamacchine ed è proprio da questa scelta di campo che sono nati i nostri nuovi piani “Esg-Energy Saving Green”. Inizia così la nostra chiacchierata con Fabrizio Azzimonti, che incontriamo negli uffici della azienda di famiglia, nota in tutto il mondo per le sue presse progettate e realizzate non solo per il mondo del legno, ma anche dei materiali compositi e ovunque ci sia bisogno di avere superfici che “stringano” un materiale per unirlo o per modificarne la forma, la struttura…
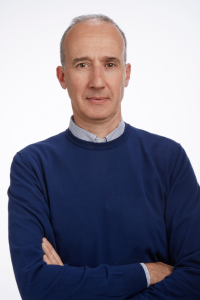
Fabrizio Azzimonti
“Il nostro sembra un comparto a basso contenuto di tecnologia, ma devo dirle che non è così e che la ricerca di modi nuovi rendere sempre più efficace le nostre macchine è continua. Abbiamo avuto l’idea di creare dei nuovi piani “green” per le nostre presse, che permettano di consumare meno energie con prestazioni per alcuni aspetti migliori”.
“Vede – prosegue Azzimonti – fino a oggi c’erano sono stati due metodi per riscaldare i piani delle “presse a caldo”: o si ricorre a sistemi che utilizzano circuiti nei quali una pompa “spinge” olio riscaldato da un boiler elettrico o si scelgono piastre di alluminio nelle quali sono annegate resistenze in rame che vengono scaldate elettricamente. Queste ultime, decisamente più energivore, sono preferite nel Nord Europa e in tutti quei Paesi dove il costo dell’energia elettrica è minore. Sono macchine che hanno una importante diffusione nelle piccole e medie falegnamerie che, a nostro avviso, sarebbero ben felici di vedere altre cifre nelle loro bollette!
Abbiamo ragionato a lungo sul problema, fino a quando non siamo entrati in contatto con una azienda che ci ha fatto comprendere che avremmo potuto utilizzare materiali diversi dal rame per scaldare i piani delle nostre presse, consumando meno energia e con una migliore distribuzione del calore sull’intera superfice.
Abbiamo usato un materiale noto, il carbonio, per creare delle nuove resistenze e avviare una serie di test che ci hanno fatto comprendere che alcune nostre esperienze, definite per le lavorazioni sui materiali compositi, avrebbero potuto esserci utili anche nel più tradizionale mondo del legno. Diciamo che abbiamo fatto centro, al punto che questi nuovi piani sono ora protetti da un brevetto d’uso e le loro prestazioni sono state certificate da Det Norske Veritas, istituto che non ha bisogno di presentazioni al quale abbiamo chiesto di misurare in modo oggettivo le prestazioni dei nostri piani “Esg”. Oramai da qualche mese stiamo dunque proponendo alle imprese di settore questo upgrade di tecnologia, sostituendo i vecchi sistemi con una soluzione che permette non solo di avere risparmi fino al 30, 40 per cento, ma potendo eliminare olio, boiler, tubazioni, rischi di perdite e costose manutenzioni… Parlando di sistemi a olio dobbiamo anche considerare che l’olio, come noto, è un derivato dal petrolio, che il suo riscaldamento genera vapori non proprio salubri e che rimane il problema dello smaltimento del fluido esausto dunque una proposta “green” anche in termini più ampi rispetto all’essere meno energivora, cosa che la rende assolutamente appetibile anche nei Paesi dove le bollette sono meno “importanti”, garantendo una maggiore redditività”.
Come ha reagito il mercato?
“Meglio di quanto potessimo attenderci. Sono oramai quasi tre anni che lavoriamo a questi nuovi piani e abbiamo diverse decine di installazioni nel mondo: già dalle prime “macchine test” abbiamo avuto segnali molto positivi e oggi riceviamo richieste da molti Paesi europei, dove esiste una sensibilità maggiore a certi temi e dove la qualità del processo deve essere massima. Non dimentichiamo che stiamo parlando di nobilitazione, della applicazione di impiallacciature o laminati – dunque dell’estetica di un prodotto – con temperature assolutamente regolabili fino a 120 gradi centigradi. Non solo: i piani “Esg” permettono all’utilizzatore di poter gestire temperature diverse, una prestazione molto interessante quando si deve nobilitare un pannello con due materiali differenti e si vuole che la parte superiore della pressa abbia una temperatura diversa da quella inferiore, cosa che con le presse a olio non è possibile ottenere… Posso anche dirle che stiamo valutando la possibilità di costruire le nostre presse “Green” anche con piani in formati diversi da quelli più diffusi, certi che ci aprirebbero nuove opportunità in altre applicazioni”.
Parliamo di prestazioni…
“Se si riferisce alla uniformità del calore sul piano posso dirle che noi abbiamo un delta fra il punto più caldo e quello più freddo di 7 gradi, dunque decisamente inferiore a quanto si registra normalmente con altri sistemi di riscaldamento. Stiamo verificando che questa maggior omogeneità permette soprattutto alle falegnameria di piccole e medie dimensioni di sperimentare impieghi diversi. Devo dire che il delta della temperatura è assolutamente adeguato anche quando si effettuano misurazioni sul numero di pressate. Mi spiego meglio: abbiamo controllato l’andamento della temperatura dei nostri piani in un normale ciclo di venti pressate, dunque aprendo e chiudendo più volte la pressa e simulando il normale lavoro quotidiano. Abbiamo così verificato che c’è un ottimo “mantenimento” della temperatura: caricando, pressando e scaricando i pannelli non perdiamo temperatura e non c’è una forte richiesta di maggior potenza per tornare alla temperatura di esercizio. La precisione nella gestione della temperatura di cui abbiamo accennato in precedenza, inoltre, rende i nostri piani “Esg” la soluzione ideale nelle presse che lavorano a ciclo continuo”.
È stato difficile raggiungere il risultato?
“Devo purtroppo dire che, dopo la fase di progettazione e le prime verifiche, abbiamo dovuto confrontarci con il problema del coronavirus: ripartire non è stato banale, soprattutto per noi che siamo in una delle zone dove la pandemia ha causato un enorme numero di vittime… Se guardiamo alla parte impiantistica posso dirle che è certamente una soluzione più semplice rispetto all’olio. La parte più difficile è stata configurare e dimensionare in modo corretto questi “tappeti” di resistenze in carbonio, bilanciando la diversa dispersione tra la parte centrale e le parti esterne dei piani: la parte esterna, più a contatto con l’aria, registra ovviamente una maggior dispersione che causa un calo della temperatura, calo che compensiamo con una diversa logica nella distribuzione delle resistenze.
Avere definito una partnership rigorosa con i nostri fornitori delle resistenze e soprattutto disporre di un ufficio tecnico capace di affrontare queste tematiche è stato indispensabile e ci aiuta tantissimo in un mercato che deve essere continuamente “stimolato”, a cui bisogna rispondere con competenza, professionalità e rigore oggettivo.
Ci è servito molto ricevere, negli ultimi diciotto mesi, i feedback dei clienti che hanno adottato questa tecnologia, segnalazioni, idee e suggerimenti che – come ho già accennato – ci hanno permesso di affinare alcuni particolari ma soprattutto di pensare a diversi e interessanti sviluppi futuri.
In questo percorso siamo stati affiancati dalla collaborazione di un laboratorio di ricerca e con il Dipartimento di scienze e innovazione tecnologica dell’Università del Piemonte Orientale, una collaborazione che continua per un progetto di ricerca, al quale prendiamo parte con il nostro fornitore, per studiare in modo ancora più approfondito le caratteristiche elettriche di queste resistenze in carbonio. Queste resistenze, infatti, non hanno un comportamento ohmico come quelle in rame, che all’aumentare della temperatura aumentano la resistenza, ma tendono a erogare più potenza con il crescere del calore, come abbiamo verificato nei nostri test.
Come le dicevo l’innovazione nasce dall’impegno continuo nella ricerca, nello sviluppo di nuove idee, e sono certo che da questa stagione così impegnativa di Ormamacchine trarremo indicazioni e idee molto concrete per il nostro futuro: posso anticiparle che, ad esempio, abbiamo studiato e verificato che lavorando sulla sezione dei fili di carbonio che sono alla base delle nostre resistenze potremmo arrivare a ottimizzare ulteriormente il risultato, creando resistenze diverse da utilizzare su macchine più grandi, possibilità che prima non avevamo, e arrivando a proporre i nostri piani “Esg” anche per i formati più usati nei Paesi anglosassoni…”.
… ma da quali comparti vi aspettate le maggiori soddisfazioni?
“La domanda più forte viene sempre dalle piccole e medie imprese, anche perchè negli ultimi anni è più forte la consapevolezza che per affrontare le profonde mutazioni del mercato bisogna investire: attualmente costruiamo circa 300/350 presse ogni anno per questa fascia di mercato, una parte importante della nostra produzione.
Mi lasci dire che sono convinto del valore di questa proposta di Ormamacchine: se pensa che in cinquant’anni l’unica evoluzione nel settore della pressatura è stata la sostituzione degli impianti di riscaldamento ad acqua, usando gli scarti di legno, con boiler elettrici o piani a resistenza… credo che noi si sia fatto un importante passo avanti, anche perché i nostri piani sono costituiti da diversi “tappeti” e in caso ci sia qualche mal funzionamento basta aprire il piano, togliere il “tappeto” e sostituirlo per riprendere immediatamente la produzione. Un vantaggio davvero enorme”.