Che il mondo della finitura richieda una grande rapidità e predisposizione al cambiamento è cosa ben nota. Lo è per il “grande pubblico”, ma lo è anche per gli addetti ai lavori. Tendenze, mode o trend, che lo si chiami all’italiana o usando un inglesismo, Nastroflex, l’azienda italiana fondata e gestita dalla famiglia Palù, ha sempre svolto un ruolo di primo piano nel mondo della finitura fin dal 1970. Cinque decadi di storia in cui in quel di Ponte di Piave ne hanno viste tante. In questi anni, infatti, si è passati dal lucido sui poliesteri degli anni Sessanta e Settanta all’opaco (prima trasparente e poi pigmentato), per poi tornare, negli anni Novanta, nuovamente alle superfici lucide. La finitura lucida è diventata un trend che, senza discontinuità, segue le evoluzioni di materiali e tecnologie e delle preferenze dei clienti. Per esempio, il lucido spazzolato ha lasciato spazio a quello che, in gergo tecnico, è definito “diretto”, ovvero con un’applicazione monostrato della vernice e una conseguente riduzione dei costi, seppure con una qualità differente.
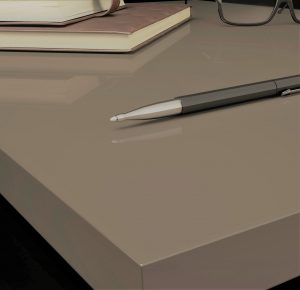
Antina lucido UV prodotta da Innova srl – www.innova-uv.it
Oggi il mercato offre molteplici soluzioni che in larga parte sono frutto di scelte e bisogni tecnico-economici, commerciali e ambientali. Le vernici applicate per cercare un punto comune tra questi bisogni sono varie. Oltre alle resine poliesteri, poliuretaniche e acriliche, sono usati anche olii naturali di impregnazione. I produttori di impianti offrono tecnologie tradizionali – ma sempre valide – come l’essicazione naturale, ad aria calda o a infrarossi accanto ad altre, i cui albori risalgono a fine anni Settanta, quali i forni “Mos” o dotati di lampade Uv a vari livelli di emissione a cui si aggiunge il recente sistema hot-melt adottato dai grandi produttori di pannelli di truciolare e mdf.
Qualsiasi sia la tecnologia adottata, il comune denominatore è l’esigenza di ottenere la cosiddetta “finitura”, lucida, semilucida o opaca che sia. E per ottenere ciò, per far sì che i risultati siano ancora più precisi, l’approccio del mondo della finitura è diventato sempre più scientifico. “Per noi la finitura equivale a piena soddisfazione del cliente o, in altre parole, ottenere il migliore risultato coniugando superficie da levigare, impianto (macchine) e aspettative, lavorando con dati oggettivi che siano misurabili e dimostrabili”, ci hanno raccontato direttamente da Nastroflex.
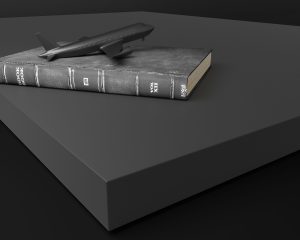
Antina opaco a eccimeri prodotta da Innova srl – www.innova-uv.it
“In pratica, ogni superficie trattata con prodotti abrasivi presenta una rugosità, definita anche scabrosità, determinata dal tipo di minerale e grana usata e della qualità complessiva dell’abrasivo. La rugosità è la responsabile della riflessione della luce su di una superficie; minore è la rugosità e maggiormente i raggi di luce che la colpiscono saranno riflessi in un unico angolo, in combinazione con la brillantezza della vernice stessa. La rugosità si misura con uno strumento, il rugosimetro, tramite una piccola punta che scorre su una porzione di area e rileva con estrema precisione picchi e avvallamenti creati dall’abrasivo. I dati rilevano soprattutto due aspetti: la rugosità media (l’indice di finitura percepita, ndr.)e i picchi di rugosità (la rilevazione del valore fra il picco più elevato e la valle più profonda del profilo, una cartina tornasole della qualità dell’abrasivo, ndr.)”.
Qualità, metodo e attenzione ai dettagli: l’approccio scientifico alla finitura di Nastroflex parte da qui.